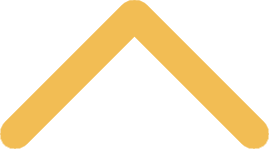
Safety: Walking-Working Surfaces
Applies to: All faculty, staff, and any contractors working on St. Norbert College property.
Purpose: To establish the minimum requirements and responsibilities for employees when on walking-working surfaces, including elevated work platforms and rooftops. This policy is designed to protect all employees engaged in work activities that expose them to risks as prescribed in the Occupational Safety and Health Administration’s (OSHA’s) Walking-Working Surfaces Standard - 29 CFR 1910.21.
Policy Owner: Human Resources
Revision Dates: February 2018, June 2018, October 2022
Last Reviewed: October 2022
Policy
RESPONSIBILITIES - The Senior Benefits and Safety Specialist shall work to identify the locations and conditions of risk to walking and working surfaces throughout the college. The Senior Benefits and Safety Specialist will also ensure that risks are mitigated and that employees are properly notified and trained on the presence of walking and working risk factors.
Department Managers shall ensure proper Personal Protective Equipment (PPE) is available, that areas requiring PPE are properly posted and that employees are held accountable for abiding by the requirements set forth in this document.
Departments - Each department’s manager is responsible for compliance with the criteria set forth in this policy. They must ensure that all elements of this policy and related procedures are implemented and followed.
Departmental Managers
- Are responsible for conducting routine inspections to ensure all walking and working surfaces are free from slip, trip, and fall hazards.
- Ensure work areas are well lit while work is in progress. Access and egress routes must be adequately lit at all times.
- Conduct training in conjuction with Human Resources for employees who use ladders, scaffolds, or other elevated platforms.
- Conduct training in use and inspection of fall prevention and fall arrest equipment.
- Ensure proper ladders are used for specific tasks.
- Provide adequate fall prevention and fall arrest equipment.
Senior Benefits and Safety Specialist
- Review changes in operations and keep current with new processes and/or facilities within the college and identify new requirements, when needed.
- Work with managers and coordinate efforts to analyze, minimize walking and working surface exposures.
- Document training records and maintain in divisions folders.
- Undertake the required reporting, investigation and administration of any walking and working surface-related incident.
- Ensure that hazard assessments have been completed to determine exposure potential and type of PPE, if any, to be used.
- Hazard assessments must be certified and signed and dated.
- Assessments will be maintained by the Sr. Benefits and Safety Specialist.
Employees
- Take part in all mandatory training associated with walking and working surface familiarization as well as to work in such a manner which reduces the possibility of having a walking and working surface incident.
- Use PPE as instructed and in accordance with training received.
- Maintain PPE and report any damage or loss to supervisor or manager.
- Maintain work areas free from slip, trip, and fall hazards.
- Correct or immediately report slip, trip, and fall hazards.
- Use proper ladders for assigned tasks.
Procedures
Housekeeping
- All work areas, passageways, storerooms, and service rooms shall be kept clean and orderly and in a sanitary condition.
- The floor of every area shall be kept as clean and dry as practical.
- Where wet processes are used, drainage shall be maintained and platforms, mats or other dry standing places shall be provided.
- Every floor, work area and passageway shall be kept free from protruding nails, splinters, holes, or loose boards.
Aisles and Passageways
- Aisles and passageways shall be kept clear and in good repair with no obstruction across or in aisles that could create a hazard.
- Permanent aisles and passageways shall be appropriately marked.
- Where mechanical handling equipment is used, sufficient safe clearances shall be allowed for aisles, at loading docks, through doorways and wherever turns or passage must be made.
Floor Loading Protection - Load rating limits shall be marked on plates and conspicuously posted. It shall be unlawful to place, or cause, or permit to be placed, on any floor or roof of a building or other structure, a load greater than that for which such floor or roof is approved.
Protection for Floor Openings
- Standard railings shall be provided on all exposed sides of a stairway opening, except at the stairway entrance. For infrequently used stairways, where traffic across the opening prevents the use of a fixed standard railing, the guard shall consist of a hinged floor opening cover of standard strength and construction along with removable standard railings on all exposed sides, except at the stairway entrance.
- A “standard railing” consists of top rail, midrail, and posts, and shall have a vertical height of 42 inches nominal from the upper surface of top rail to floor, platform, runway, or ramp level. Nominal height of mid rail is 21 inches.
- A “standard toeboard” is 4 inches nominal in vertical height, with not more than ¼ inch clearance above floor level.
- Floor openings may be covered rather than guarded with rails. When the floor opening cover is removed, a temporary guardrail shall be in place, or an attendant shall be stationed at the opening to warn personnel.
- Every floor hole into which persons can accidentally walk shall be guarded by either:
- A standard railing with toeboard.
- A floor hole cover of standard strength and construction.
- While the cover is not in place, the floor hole shall be constantly attended by someone or shall be protected by a removable standard railing.
Protection of Open-Sided Floors, Platforms, and Runways
- Every open-sided floor or platform 4 feet or more above adjacent floor or ground level shall be guarded by a standard railing on all open sides, except where there is an entrance to a ramp, stairway, or fixed ladder.
- The railing shall be provided with a toeboard whenever:
- Persons can pass.
- There is moving machinery.
- There is equipment with which falling materials could create a hazard.
- Every runway shall be guarded by a standard railing, or the equivalent, on all sides 4 feet or more above floor or ground level. Wherever tools, machine parts, or materials are likely to be used on the runway, a toeboard shall also be provided on each exposed side.
Stairway Railings and Guards
- Every flight of stairs with four or more risers shall have standard stair railing or handrails as specified below. Stair width is measured clear of all obstructions except handrails. On stairways less than 44 inches wide having both sides enclosed, at least one handrail shall be affixed, preferably on the right side descending.
- On stairways less than 44 inches wide with one open side, at least one stair rail shall be affixed on the open side.
- On stairways less than 44 inches wide having both sides open, two stair rails shall be provided, one for each side.
- On stairways more than 44 inches wide, by less than 88 inches, one handrail shall be provided on each enclosed side and one stair rail on each open side.
- On stairways 88 inches or more in width, one handrail shall be provided on each enclosed side, one stair rail on each open side, and one intermediate stair rail placed approximately in the middle of the stairs.
- A “standard stair railing” shall be of construction similar to a standard railing, but the vertical height shall be not more than 34 inches nor less than 30 inches from the upper surface of the top rail to the surface of the tread in line with the face of the riser at the forward edge of the tread.
Fixed Industrial Stairs - Fixed industrial stairs shall be provided for access to and from places of work where operations necessitate regular travel between levels. Requirements include:
- Fixed industrial stairs shall be strong enough to carry five times the normal anticipated live load.
- At the very minimum, any fixed stairway shall be able to carry safely a moving concentrated load of 1000 pounds.
- All fixed stairways shall have a minimum width of 22 inches.
- Fixed stairs shall be installed at angles to the horizontal of between 30 degrees and 50 degrees.
- Vertical clearance above any stair tread to an overhead obstruction shall be at least 7 feet measured from the leading edge of the tread.
Portable Ladders
- The chief hazard when using a ladder is falling. A poorly designed, maintained, or improperly used ladder may collapse under the load placed upon it and cause the employee to fall.
- A ladder is an appliance consisting of two side rails joined at regular intervals by cross pieces on which a person may step to ascend or descend.
- The various types of portable ladders include:
- Stepladder – A self-supporting portable ladder, non-adjustable in length, having flat steps and hinged back.
- Single Ladder – A non self-supporting portable ladder, non adjustable in length, consisting of but one section. Its size is designed by overall length of the side rail.
- Extension Ladder – A non self-supporting portable ladder adjustable in length.
- Portable ladder requirements:
- Portable step ladders longer than 20 feet shall not be used.
- Step Ladders shall be equipped with a spreader or locking device of sufficient size and strength to securely hold the front and back sections in open position.
- Single ladders longer than 30 feet shall not be used.
- Extension ladders longer than 60 feet shall not be used.
- Ladders shall be maintained in good condition at all times.
- Ladders shall be inspected before each use and those, which have developed defects, shall be withdrawn from service for repair or destruction and tagged or marked as “Dangerous, Do Not Use.” When discarding a ladder, it must be destroyed in such a manner as to render it useless. Another person must not be given the opportunity to use a ladder that has been deemed unsafe.
- Portable ladder safety precautions:
- Ladders shall be placed with a secure footing, or they shall be lashed, or held in position.
- Ladders used to gain access to a roof or other area shall extend at least 3 feet above the point of support.
- The foot of a ladder, shall be at such a pitch that the horizontal distance from the top support to the foot of the ladder, is one-quarter of the working length of the ladder.
- The worker shall always face the ladder when climbing up or down.
- Short ladders shall not be spliced together to make long ladders.
- Ladders shall never be used in the horizontal position as scaffolds or work platforms.
- The top of a regular stepladder shall not be used as a step.
- Use both hands when climbing and descending ladders.
- Aluminum ladders shall not be used near electrical equipment.
- A personal fall arrest system is mandatory and must be used anytime work is done over 6 feet, regardless of how long the task will take.
- A personal fall arrest system is not required when ascending or descending to the required work platforms.
- When using a personal fall arrest system on a ladder, do not tie off to the ladder itself.
Fixed Ladders - A fixed ladder is a ladder permanently attached to a structure, building or equipment. Fixed ladders with a length of more than 20 feet to a maximum unbroken length of 30 feet shall be equipped with cages or a ladder safety device.
- A “cage” is a guard that is fastened to the side rails of the fixed ladder or to the structure to encircle the climbing space of the ladder for the safety of the person who must climb the ladder.
- Cages shall extend a minimum of 42 inches above the top of a landing, unless other acceptable protection is provided.
- Cages shall extend down the ladder to a point not less than 7 feet nor more than 8 feet above the base of the ladder.
Scaffolds
- The footing or anchorage for scaffolds shall be sound, rigid and capable of carrying the maximum intended load without settling or displacement.
- Unstable objects, such as barrels, boxes, loose brick, or concrete blocks shall not be used to support scaffolds or planks.
- Scaffolds and their components shall be capable of supporting at least four times the maximum intended load.
- Scaffolds shall be maintained in a safe condition and shall not be altered or moved horizontally while they are in use or occupied.
- Damaged or weakened scaffolds shall be immediately repaired and shall not be used until repairs have been completed.
- A safe means must be provided to gain access to the working platform level through the use of a ladder, ramp, etc.
- Overhead protection must be provided for personnel on a scaffold exposed to overhead hazards (this may include, but is not limited to; hardhats, eye protection, electric-resistant gloves and guards).
- Guardrails, midrails, and toeboards must be installed on all open sides and ends of platforms more than 10 feet above the ground or floor. Wire mesh must be installed between the toeboard and the guardrail along the entire opening, where persons are required to work or pass under the scaffolds.
- Employees shall not work on scaffolds during storms or high winds or when covered with ice or snow.
POLICY EVALUATION - The Senior Benefits and Safety Specialist will conduct periodic evaluations of the workplace to ensure that the provisions of this policy are being implemented. The evaluation will include regular consultations with employees who work on and/or around walking and working surfaces, their supervisors, site inspections and review of records. Identified problems will be noted and addressed by the Senior Benefits and Safety Specialist.
DOCUMENTATION AND RECORDKEEPING - Training records will be retained in Workday. These records will be updated as new employees are trained and as existing employees receive refresher training.
Policy
RESPONSIBILITIES - The Senior Benefits and Safety Specialist shall work to identify the locations and conditions of risk to walking and working surfaces throughout the college. The Senior Benefits and Safety Specialist will also ensure that risks are mitigated and that employees are properly notified and trained on the presence of walking and working risk factors.
Department Managers shall ensure proper Personal Protective Equipment (PPE) is available, that areas requiring PPE are properly posted and that employees are held accountable for abiding by the requirements set forth in this document.
Departments - Each department’s manager is responsible for compliance with the criteria set forth in this policy. They must ensure that all elements of this policy and related procedures are implemented and followed.
Departmental Managers
- Are responsible for conducting routine inspections to ensure all walking and working surfaces are free from slip, trip, and fall hazards.
- Ensure work areas are well lit while work is in progress. Access and egress routes must be adequately lit at all times.
- Conduct training in conjuction with Human Resources for employees who use ladders, scaffolds, or other elevated platforms.
- Conduct training in use and inspection of fall prevention and fall arrest equipment.
- Ensure proper ladders are used for specific tasks.
- Provide adequate fall prevention and fall arrest equipment.
Senior Benefits and Safety Specialist
- Review changes in operations and keep current with new processes and/or facilities within the college and identify new requirements, when needed.
- Work with managers and coordinate efforts to analyze, minimize walking and working surface exposures.
- Document training records and maintain in divisions folders.
- Undertake the required reporting, investigation and administration of any walking and working surface-related incident.
- Ensure that hazard assessments have been completed to determine exposure potential and type of PPE, if any, to be used.
- Hazard assessments must be certified and signed and dated.
- Assessments will be maintained by the Sr. Benefits and Safety Specialist.
Employees
- Take part in all mandatory training associated with walking and working surface familiarization as well as to work in such a manner which reduces the possibility of having a walking and working surface incident.
- Use PPE as instructed and in accordance with training received.
- Maintain PPE and report any damage or loss to supervisor or manager.
- Maintain work areas free from slip, trip, and fall hazards.
- Correct or immediately report slip, trip, and fall hazards.
- Use proper ladders for assigned tasks.
Procedures
Housekeeping
- All work areas, passageways, storerooms, and service rooms shall be kept clean and orderly and in a sanitary condition.
- The floor of every area shall be kept as clean and dry as practical.
- Where wet processes are used, drainage shall be maintained and platforms, mats or other dry standing places shall be provided.
- Every floor, work area and passageway shall be kept free from protruding nails, splinters, holes, or loose boards.
Aisles and Passageways
- Aisles and passageways shall be kept clear and in good repair with no obstruction across or in aisles that could create a hazard.
- Permanent aisles and passageways shall be appropriately marked.
- Where mechanical handling equipment is used, sufficient safe clearances shall be allowed for aisles, at loading docks, through doorways and wherever turns or passage must be made.
Floor Loading Protection - Load rating limits shall be marked on plates and conspicuously posted. It shall be unlawful to place, or cause, or permit to be placed, on any floor or roof of a building or other structure, a load greater than that for which such floor or roof is approved.
Protection for Floor Openings
- Standard railings shall be provided on all exposed sides of a stairway opening, except at the stairway entrance. For infrequently used stairways, where traffic across the opening prevents the use of a fixed standard railing, the guard shall consist of a hinged floor opening cover of standard strength and construction along with removable standard railings on all exposed sides, except at the stairway entrance.
- A “standard railing” consists of top rail, midrail, and posts, and shall have a vertical height of 42 inches nominal from the upper surface of top rail to floor, platform, runway, or ramp level. Nominal height of mid rail is 21 inches.
- A “standard toeboard” is 4 inches nominal in vertical height, with not more than ¼ inch clearance above floor level.
- Floor openings may be covered rather than guarded with rails. When the floor opening cover is removed, a temporary guardrail shall be in place, or an attendant shall be stationed at the opening to warn personnel.
- Every floor hole into which persons can accidentally walk shall be guarded by either:
- A standard railing with toeboard.
- A floor hole cover of standard strength and construction.
- While the cover is not in place, the floor hole shall be constantly attended by someone or shall be protected by a removable standard railing.
Protection of Open-Sided Floors, Platforms, and Runways
- Every open-sided floor or platform 4 feet or more above adjacent floor or ground level shall be guarded by a standard railing on all open sides, except where there is an entrance to a ramp, stairway, or fixed ladder.
- The railing shall be provided with a toeboard whenever:
- Persons can pass.
- There is moving machinery.
- There is equipment with which falling materials could create a hazard.
- Every runway shall be guarded by a standard railing, or the equivalent, on all sides 4 feet or more above floor or ground level. Wherever tools, machine parts, or materials are likely to be used on the runway, a toeboard shall also be provided on each exposed side.
Stairway Railings and Guards
- Every flight of stairs with four or more risers shall have standard stair railing or handrails as specified below. Stair width is measured clear of all obstructions except handrails. On stairways less than 44 inches wide having both sides enclosed, at least one handrail shall be affixed, preferably on the right side descending.
- On stairways less than 44 inches wide with one open side, at least one stair rail shall be affixed on the open side.
- On stairways less than 44 inches wide having both sides open, two stair rails shall be provided, one for each side.
- On stairways more than 44 inches wide, by less than 88 inches, one handrail shall be provided on each enclosed side and one stair rail on each open side.
- On stairways 88 inches or more in width, one handrail shall be provided on each enclosed side, one stair rail on each open side, and one intermediate stair rail placed approximately in the middle of the stairs.
- A “standard stair railing” shall be of construction similar to a standard railing, but the vertical height shall be not more than 34 inches nor less than 30 inches from the upper surface of the top rail to the surface of the tread in line with the face of the riser at the forward edge of the tread.
Fixed Industrial Stairs - Fixed industrial stairs shall be provided for access to and from places of work where operations necessitate regular travel between levels. Requirements include:
- Fixed industrial stairs shall be strong enough to carry five times the normal anticipated live load.
- At the very minimum, any fixed stairway shall be able to carry safely a moving concentrated load of 1000 pounds.
- All fixed stairways shall have a minimum width of 22 inches.
- Fixed stairs shall be installed at angles to the horizontal of between 30 degrees and 50 degrees.
- Vertical clearance above any stair tread to an overhead obstruction shall be at least 7 feet measured from the leading edge of the tread.
Portable Ladders
- The chief hazard when using a ladder is falling. A poorly designed, maintained, or improperly used ladder may collapse under the load placed upon it and cause the employee to fall.
- A ladder is an appliance consisting of two side rails joined at regular intervals by cross pieces on which a person may step to ascend or descend.
- The various types of portable ladders include:
- Stepladder – A self-supporting portable ladder, non-adjustable in length, having flat steps and hinged back.
- Single Ladder – A non self-supporting portable ladder, non adjustable in length, consisting of but one section. Its size is designed by overall length of the side rail.
- Extension Ladder – A non self-supporting portable ladder adjustable in length.
- Portable ladder requirements:
- Portable step ladders longer than 20 feet shall not be used.
- Step Ladders shall be equipped with a spreader or locking device of sufficient size and strength to securely hold the front and back sections in open position.
- Single ladders longer than 30 feet shall not be used.
- Extension ladders longer than 60 feet shall not be used.
- Ladders shall be maintained in good condition at all times.
- Ladders shall be inspected before each use and those, which have developed defects, shall be withdrawn from service for repair or destruction and tagged or marked as “Dangerous, Do Not Use.” When discarding a ladder, it must be destroyed in such a manner as to render it useless. Another person must not be given the opportunity to use a ladder that has been deemed unsafe.
- Portable ladder safety precautions:
- Ladders shall be placed with a secure footing, or they shall be lashed, or held in position.
- Ladders used to gain access to a roof or other area shall extend at least 3 feet above the point of support.
- The foot of a ladder, shall be at such a pitch that the horizontal distance from the top support to the foot of the ladder, is one-quarter of the working length of the ladder.
- The worker shall always face the ladder when climbing up or down.
- Short ladders shall not be spliced together to make long ladders.
- Ladders shall never be used in the horizontal position as scaffolds or work platforms.
- The top of a regular stepladder shall not be used as a step.
- Use both hands when climbing and descending ladders.
- Aluminum ladders shall not be used near electrical equipment.
- A personal fall arrest system is mandatory and must be used anytime work is done over 6 feet, regardless of how long the task will take.
- A personal fall arrest system is not required when ascending or descending to the required work platforms.
- When using a personal fall arrest system on a ladder, do not tie off to the ladder itself.
Fixed Ladders - A fixed ladder is a ladder permanently attached to a structure, building or equipment. Fixed ladders with a length of more than 20 feet to a maximum unbroken length of 30 feet shall be equipped with cages or a ladder safety device.
- A “cage” is a guard that is fastened to the side rails of the fixed ladder or to the structure to encircle the climbing space of the ladder for the safety of the person who must climb the ladder.
- Cages shall extend a minimum of 42 inches above the top of a landing, unless other acceptable protection is provided.
- Cages shall extend down the ladder to a point not less than 7 feet nor more than 8 feet above the base of the ladder.
Scaffolds
- The footing or anchorage for scaffolds shall be sound, rigid and capable of carrying the maximum intended load without settling or displacement.
- Unstable objects, such as barrels, boxes, loose brick, or concrete blocks shall not be used to support scaffolds or planks.
- Scaffolds and their components shall be capable of supporting at least four times the maximum intended load.
- Scaffolds shall be maintained in a safe condition and shall not be altered or moved horizontally while they are in use or occupied.
- Damaged or weakened scaffolds shall be immediately repaired and shall not be used until repairs have been completed.
- A safe means must be provided to gain access to the working platform level through the use of a ladder, ramp, etc.
- Overhead protection must be provided for personnel on a scaffold exposed to overhead hazards (this may include, but is not limited to; hardhats, eye protection, electric-resistant gloves and guards).
- Guardrails, midrails, and toeboards must be installed on all open sides and ends of platforms more than 10 feet above the ground or floor. Wire mesh must be installed between the toeboard and the guardrail along the entire opening, where persons are required to work or pass under the scaffolds.
- Employees shall not work on scaffolds during storms or high winds or when covered with ice or snow.
POLICY EVALUATION - The Senior Benefits and Safety Specialist will conduct periodic evaluations of the workplace to ensure that the provisions of this policy are being implemented. The evaluation will include regular consultations with employees who work on and/or around walking and working surfaces, their supervisors, site inspections and review of records. Identified problems will be noted and addressed by the Senior Benefits and Safety Specialist.
DOCUMENTATION AND RECORDKEEPING - Training records will be retained in Workday. These records will be updated as new employees are trained and as existing employees receive refresher training.
Contact Us
Location
Our office is located on First Street in the Garden Level (lower level) of Main Hall in De Pere, Wis.
Campus Map
Hours of Operation
Monday-Friday
8 a.m.-4:30 p.m.
Phone: 920-403-3211
Fax: 920-403-3983
Email: hr@snc.edu